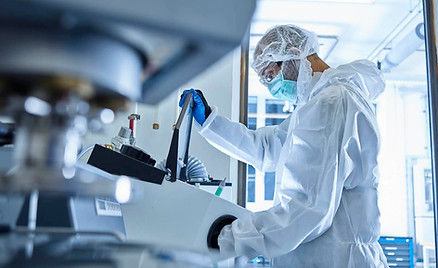
Cleanroom Testing
Cleanrooms utilize HEPA-filtered air along with predetermined airflow patterns and parameters to minimize potential contamination; to control the concentration of airborne particulates; and to ensure appropriate environmental conditions in critical zones withing the working areas. Cleanrooms may be designed to function as positive or negative pressure environments, requiring specific air differential metrics.
All cleanroom testing is performed by highly qualified technicians in accordance with current good manufacturing practices [cGMP], Institute of Environmental Sciences Technologies [IEST], International Organization for Standardization [ISO], and any applicable customer design specifications. Each cleanroom testing and certification event is reported with complete diagrammatic processes, procedures and results, to include final evaluation and recommendations.
​
Standard Testing Performed:
-
Airflow volume/velocity readings – measures unidirectional and non-unidirectional flow characteristics and ensure appropriate air patterns are maintained in unidirectional areas.
-
Room Air Exchange Rate – confirms room air exchanges per hour to ensure proper ventilation rates.
-
Temperature/relative humidity measurement – Identifies whether HVAC controls are functioning properly and uniformly providing appropriate temperature and relative humidity consistent with standards.
-
Room differential pressure testing – verifies room differential pressures meet requirements.
-
HEPA filter testing – Ensures that HEPA filter functionality in clean rooms provide required filtration in accordance with standards.
-
Non-viable particulate counts – Identifies the amount of airborne particulate of a specified size in the clean zone consistent with ISO 14644 or EU Annex 1 guidance.
Additional Testing and Services:
-
Air Balancing – adjusts airflow through the air handling systems to balance and maintain airflow, room air exchange rates, and pressure differential.
-
Airflow Visualization Studies – qualitatively verifies airflow direction using a source of visualization.
-
Viable Environmental Contamination Monitoring – performed on both air and surfaces to determine if bacterial and/or fungal contamination is evident.
-
Employee Safety and Comfort Tests – Lighting, Vibration, and Ambient Sound Testing.​​

Biosafety Cabinets
Our organization provides biosafety cabinet testing and certification which is compliant with federal safety guidelines. Each biosafety cabinet certification is accomplished with NSF Accredited Field Certifiers present at your facility.
Biological safety cabinets (BSCs) are field tested in accordance with NSF/ANSI 49, OSHA, NIH/CDC, consistent with manufacturer's specifications. NSF 49 recommends that certifications should take place at least every 12 months. In addition to that, certification of performance should be accomplished whenever biosafety cabinet units are installed, relocated or have undergone significant maintenance such as replacement of HEPA filtration. A more stringent time table of semiannual testing should be performed where the equipment is used in a cGMP environment. BioAssurance can consult with your organization to develop a testing program which will consistently meet appropriate standards of compliance.
​
Standard tests performed:
-
Inflow and Downflow Velocity Measurements – determines if proper, unidirectional airflow is maintained preventing contamination of product, operator and environment.
-
HEPA Filter Integrity – ensures that proper filtration is in place to prevent contamination.
-
Smoke Pattern Testing – visually verifies airflow direction.
-
Installation Testing and Alarm Calibration – assesses alarm performance for NSF and OSHA worksite compliance.
Additional tests:
-
Non-Viable Particle Counts – performed in accordance with ISO 14644-1 or EC Annex 1.
-
Viable Environmental Monitoring – air sampling for bacterial and fungal contamination according to client requirements
-
Fluorescent Light Testing – ensures fluorescent lighting levels consistent with standards.
-
Employee Safety and Comfort Tests – Lighting, Vibration, and Ambient Sound Testing.
-
Airflow Visualization Studies – provides identification of appropriate work zones to mitigate contamination risk.
-
Hazardous Drug Exposure Testing – Consistent with USP 825 standards

Chemical Fume Hood
/ASHRAE-110
Chemical Fume Hood viability is critical to the provision of a safe working environment ensuring exposure prevention for operator personnel. Ongoing assessment of CFH equipment is ongoing and should include daily cleaning and visual inspection for any possible air flow restriction. In addition, calibrated airflow alarms (auditory and visual) should be present to ensure a safe working environment.
Testing and certification of CFHs should be accomplished annually at minimum. In addition, testing should be done at installation of the equipment as well as recertification at any time the CFH is altered or moved. All testing is accomplished by credentialed technicians utilizing state of the art, calibrated equipment consistent with regulations and standards set forth in ASHRAE-110, OSHA, SEFA 1 and AIHA/ANSI guidance. Sulfur hexafluoride is utilized for tracer gas testing consistent with ASHRAE Standard 110.
​
Standard Testing Performed:
-
Smoke Visualization Testing – determines air capture characteristics at the face of the CFH.
-
Inflow Face Air Velocity Testing – determines air flow at the unit face.
-
Tracer Gas Containment Testing – quantifies the containment performance of the CFH.
Additional Testing and Services:
-
Employee Safety and Comfort Tests – Lighting, Vibration, and Ambient Sound Testing.
-
Sash Motion Tracer Gas Testing
-
Cross-Draft Testing
-
Variable and Constant Air Volume Testing
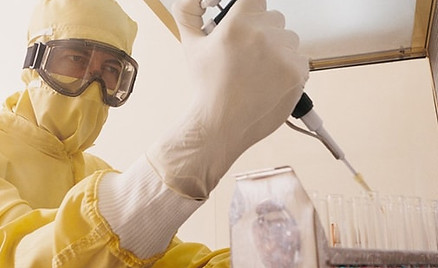
Clean Bench/ Laminar
Validation of clean bench and laminar air flow work space viability within federal standards is critical to reducing contamination. BCET performs comprehensive testing, certification and maintenance of unidirectional flow systems (laminar air flow units or clean bench environments). All laminar flow hood testing and clean bench testing is performed in accordance with applicable federal and international guidelines, current good manufacturing practices [cGMPs], and device specifications.
Laminar flow unit testing/clean bench testing and certification are performed in accordance with IEST and manufacturers' specifications.
Primary testing:
-
HEPA Filter Integrity – testing for leakage or defects in HEPA functionality to determine that no contamination will enter the work surface through filtration
-
Airflow Velocity Profile – documents the air in the work area is unidirectional and performing according to specifications, preventing cross contamination
-
Light Testing – determines if lighting levels are sufficient and UV lighting operates adequately
-
Viable Environmental Monitoring – air sampling for bacterial and fungal contamination
-
Smoke Pattern Testing – visualization to ensure proper air flow distribution
Additional testing:
-
Non-Viable Particle Counts – performed in accordance with ISO 14644-1 or EC Annex 1 and reports the amount of particulate, if any, within the work zone
-
Media Fill Exposure Testing – verification of aseptic technique utilized by technicians engaged in work within the environment following USP 797 standards
-
Glove Fingertip Testing - verification of aseptic technique utilized by technicians engaged in work within the environment following USP 797 standards
-
Vibration Testing – ensures product is not subject to damage due to vibration
-
Sound Testing – verifies hood operation/usage does not exceed standards
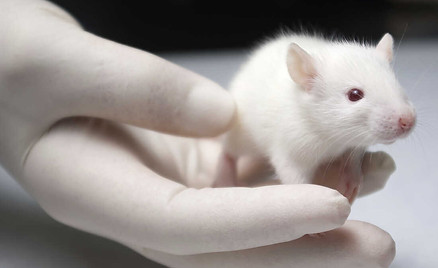
Animal Biosafety
Our certified professionals provide testing of animal research enclosures, habitats, cage racks and changing stations, and other HEPA filtered and ventilated enclosed animal environments. Testing is performed to ensure the safety of both the research animals as well as the researchers. Testing and certification of each ventilated and filtered animal research enclosure is accomplished with NSF Accredited Field Certifiers present at your facility.
Standard tests performed:
-
Inflow and Downflow Velocity Measurements – determines if proper, unidirectional airflow is maintained preventing contamination of research subject, operator and environment
-
HEPA Filter Integrity – ensures that proper filtration is in place to prevent contamination
-
Room Air Exchange Rate – confirms room air exchanges per hour to ensure proper ventilation rates.
-
Installation Testing and Alarm Calibration – assesses alarm performance for NSF and OSHA worksite compliance
-
Room differential pressure testing – verifies room differential pressures meet requirements.
Additional tests:
-
Non-Viable Particle Counts – performed in accordance with ISO 14644-1 to determine particulate in the working area
-
Fluorescent Light Testing – ensures fluorescent lighting levels consistent with standards
-
UV Light Testing
-
Unit Vibration Testing
-
Sound Testing - ensures hood operation/usage is consistent with standards for exposure
-
Airflow Visualization Studies – provides identification of appropriate work zones to mitigate contamination risk

Negative Pressure
Negative pressure environments are necessary in healthcare settings to contain known or suspected contaminates, particularly in procedure areas or patient habitats. Specifically, air flow parameters must follow specified levels of differential pressure through each threshold (external, ante room and negative pressure room) to reduce potential outside environmental contamination.
All negative pressure room testing is performed by highly qualified technicians in accordance with national standards and applicable customer design specifications. Each negative pressure room certification event is reported with complete diagrammatic processes, procedures and results, to include final evaluation and recommendations.
Standard Testing Performed:
-
Airflow Volume/Velocity Readings – measures unidirectional and non-unidirectional flow characteristics throughout all thresholds to ensure flow characteristics are appropriate.
-
Air Exchanges Per Hour (AEPH) – confirms room air exchanges per hour to ensure proper ventilation rates.
-
Room Differential Pressure Testing – verifies room differential pressures meet requirements.
-
HEPA filter testing – Ensures that HEPA filter functionality in negative pressure rooms provide required exit recirculation filtration on the outflow of air in accordance with standards.
Additional Testing and Services:
-
Air Balancing – adjusts airflow through the air handling systems to balance and maintain airflow, room air exchange rates, and pressure differential.
-
Airflow Visualization Studies – qualitatively verifies airflow direction using a source of visualization.
-
Viable Environmental Contamination Monitoring – performed on both air and surfaces to determine if bacterial and/or fungal contamination is evident outside the negative pressure environment.

Surgery & Procedure
Surgery suites and procedure rooms utilize HEPA-filtered air along with predetermined airflow patterns and parameters to minimize potential contamination; to control the concentration of airborne particulates; and to ensure appropriate environmental conditions in critical zones withing the working areas. Surgery/procedure rooms may be designed to function as positive or negative pressure environments, requiring specific air differential metrics.
All surgery and procedure room testing is performed by highly qualified technicians in accordance national standards as well as applicable client design specifications. The surgery and procedure room certification event is reported with complete diagrammatic processes, procedures and results, to include final evaluation and recommendations.
Standard Testing Performed:
-
Airflow volume/velocity readings – measures unidirectional and non-unidirectional flow characteristics and ensure appropriate air patterns are maintained in unidirectional areas.
-
Room Air Exchange Rate – confirms room air exchanges per hour to ensure proper ventilation rates.
-
Temperature/relative humidity measurement – Identifies whether HVAC controls are functioning properly and uniformly providing appropriate temperature and relative humidity consistent with standards.
-
Room differential pressure testing – verifies room differential pressures meet requirements.
-
HEPA filter testing – Ensures that HEPA filter functionality in surgery/procedure rooms provide required filtration in accordance with standards.
-
Non-viable particulate counts – Identifies the amount of airborne particulate of a specified size in the clean zone consistent with ISO 14644 or EU Annex 1 guidance.
Additional Testing and Services:
-
Air Balancing – adjusts airflow through the air handling systems to balance and maintain airflow, room air exchange rates, and pressure differential.
-
Airflow Visualization Studies – qualitatively verifies airflow direction using a source of visualization.
-
Viable Environmental Contamination Monitoring – performed on both air and surfaces to determine if bacterial and/or fungal contamination is evident.
-
Employee Safety and Comfort Tests – Lighting, Vibration, and Ambient Sound Testing.